Методы и устройства для ультразвукового контроля качества сварных соединений полученных электродуговой сваркой, сваркой трением, сваркой взрывом, магнитоимпульсной сваркой и др.
Сегодня, сварка является одним из основных технологических процессов применяющихся при изготовлении различных конструкций. Качество сварных соединений определяет качество и надежность конструкций в целом. К сожалению, технологический процесс сварки не всегда обеспечивает должное качество сварного соединения. Кроме того, в ряде случаев существует тенденция к развитию дефектов в сварных соединениях в период эксплуатации. Поэтому развитие средств контроля и диагностики сварки остается актуальной задачей.
В лаборатории, по заказам заинтересованных организаций проводятся разработки средств контроля различных сварных соединений, включая аппаратное обеспечение, первичные преобразователи, методики контроля (электродуговая сварка, сварка трением, сварка взрывом, магнитоимпульсная сварка и т.д.). Наряду с этим выполняются работы по контролю качества различных покрытий и их адгезии к основному материалу, включая контроль баббитовых подшипников.
Примеры разработок:
Электродуговая сварка
Контроль качества сварки фланца картера заднего моста грузовых автомобилей
Контроль осуществляется со стороны наружной поверхности фланца. Для этого используется переносное устройство, которое закрепляется на торцевой поверхности фланца моста (Рис.1: 1- сварной шов; 2- само измерительное устройство; 3- привод сканирования). Устройство содержит первичный преобразователь и систему сканирования. Сканирование можно осуществлять как вручную, так и с использованием шагового двигателя. Определяется место расположения дефекта для последующего ремонта. Эффект достигается за счет специальной конструкции преобразователя. Время контроля одного фланца не превышает 5 минут. Удобство заключается в в том, что устройство переносится от моста к мосту в условиях их хранения. Нет необходимости транспотировать мост в измерительную лабораторию или на пост контроля.
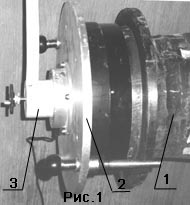
Контроль стыковых и тавровых соединений арматуры:
Разработан прибор (рис.1), состоящий из электронного блока,и приспособлений для крепления датчиков и самих датчиков, реализующий способ ультразвукового неразрушающего определенный ГОСТ 23858-71. «Соединения сварные стыковые и тавровые арматуры железобетонных конструкций. Ультразвуковые методы контроля качества. Правила приемки». Использование современной электронной базы и прогресс, достигнутый в области обработки результатов измерений позволили упростить процесс контроля арматуры и сделать его доступным для производства без необходимости привлечения высококвалифицированной рабочей силы
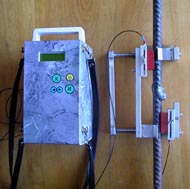
Сварка трением
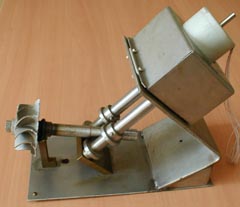
Опыт практического применения сварки трением показывают, что ее целесообразно применять для сварки деталей диаметром от 6 до 100 мм. Наиболее эффективно применение сварки трением для изготовления режущего инструмента, при производстве составных сварно-кованых, сварно-литых или сварно-штампованных деталей. Она оказывается незаменимой при соединении трудносвариваемых или вовсе не сваривающихся другими способами разнородных материалов, например, стали с алюминием, аустенитных сталей с перлитными. Нами разработаны средства автоматизированного контроля сварных соединений заготовок концевого металлорежущего инструмента, роторов турбокомпрессоров и клапанов двигателей внутреннего сгорания. Контроль позволяет выявлять дефекты периферийного кольцевого непровара, дефекты «блестящие кольца» и другие. Контроль проводится до операции снятия грата и позволяет оценить относительную площадь непровара.
Сварка взрывом, магнитоимпульсная сварка, наплавка, напыление и аналогичные технологические процессы применяются в основном для соединения разнородных материалов (биметаллов). Мы имеем опыт создания специальных технических средств для контроля изделий с различной конфигурацией – плоскость, внутренняя поверхность цилиндра, сфера (шаровой палец) и т.д. В любом случае предложенный метод и оборудование позволяют оценить площадь непровара.